We believe in innovation and love modern technologies.
Smart manufacturing is the way we give all our passion for.
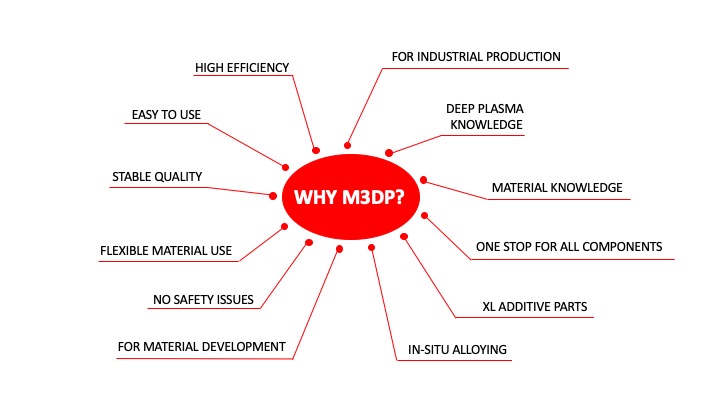
Additive Manufacturing of large metal structures often refers to WAAM® or Wire Arc Additive Manufacturing. Our System uses a Direct Energy Deposition (DED) technology, that is flexible to use a single wire, multi wires or even powders as feedstock for the additive building process. We call this technology Plasma Metal Deposition - PMD, using a plasma torch as the heat source. Plasma welding has the advantage of an excellent weld pool control, with high stability for the energy impact independent to the distance range between torch and building platform.
When it comes to material properties in Additive Manufacturing, it is essential to understand all parts of the metallurgical build-up process. SBI knows how to build their own power sources, tune the electronics and customize the plasma arc characteristics. That's why RHP has chosen SBI as the partner for innovative future developments to be based on Plasma Metal Deposition AM.
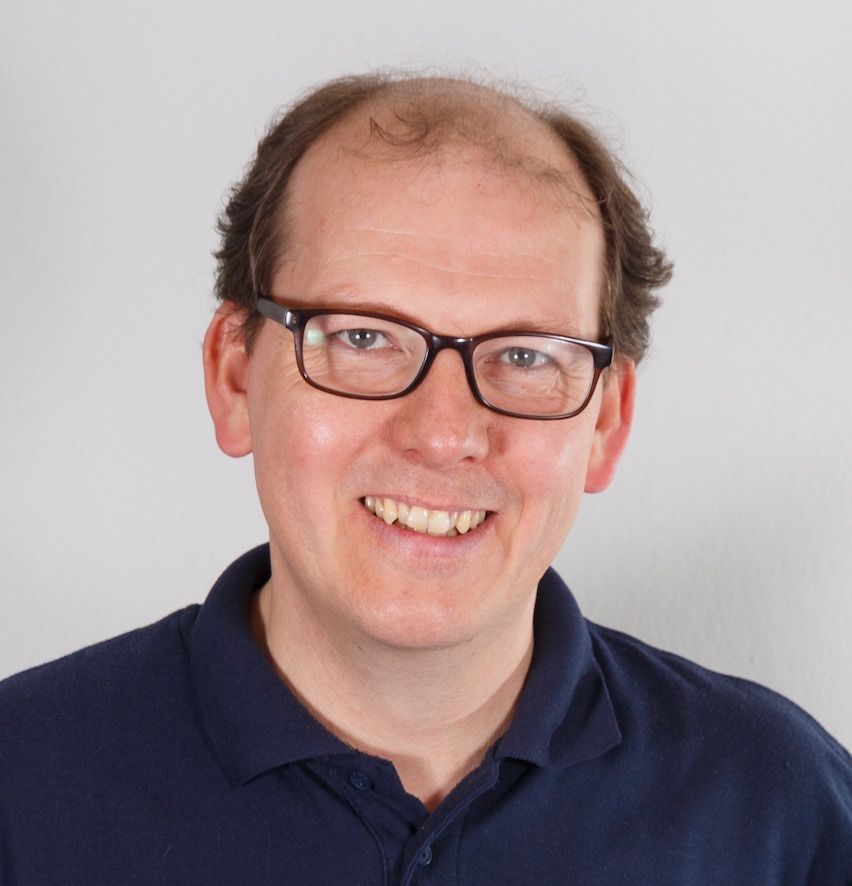
Our M3DP AM machines are CNC guided SBI plasma printing systems for Wire Arc Additive Manufacturing and Powder Arc Additive Manufacturing. The plasma torch is moved by a CNC gantry system along an arbitrary path and creates a weld pool on a substrate plate. By adding wire into the weld pool material deposition is achieved. Putting one deposition over the previous a desired part can be generated.

M3DP
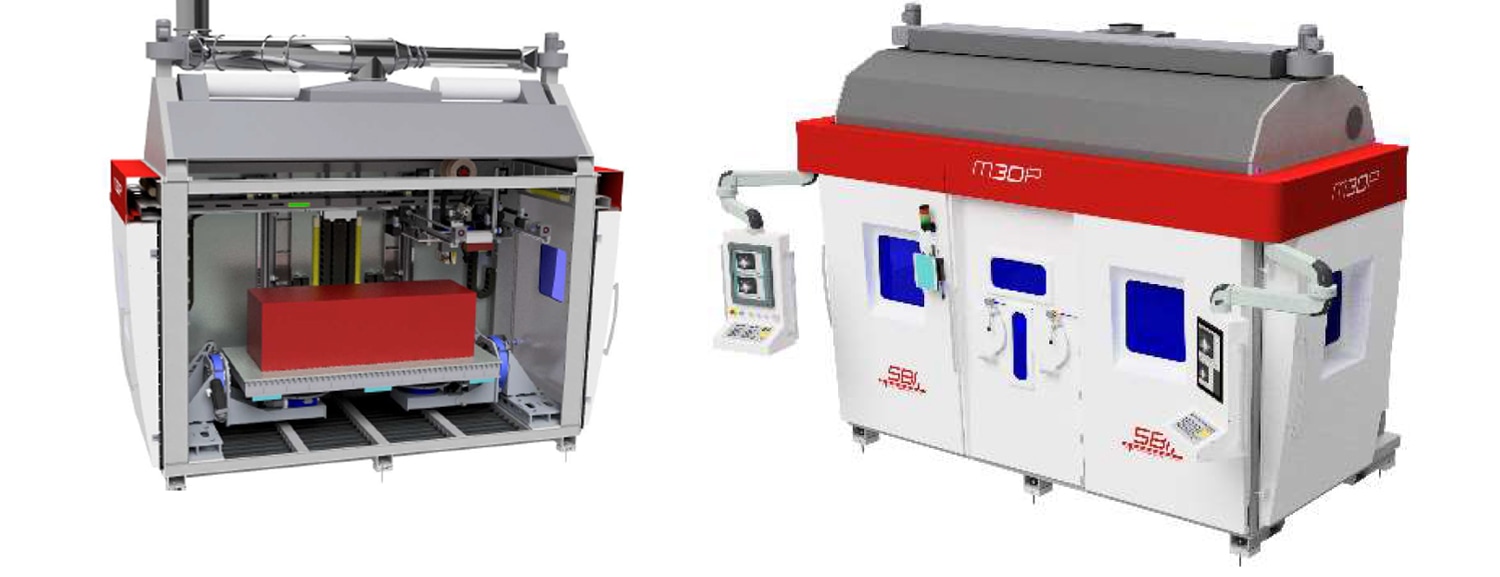
The SBI Additive Manufacturing Machine for highly productive industrial use. Quality control, data collection and easy use make this machine the best in class for large AM parts.
M3DP-SL
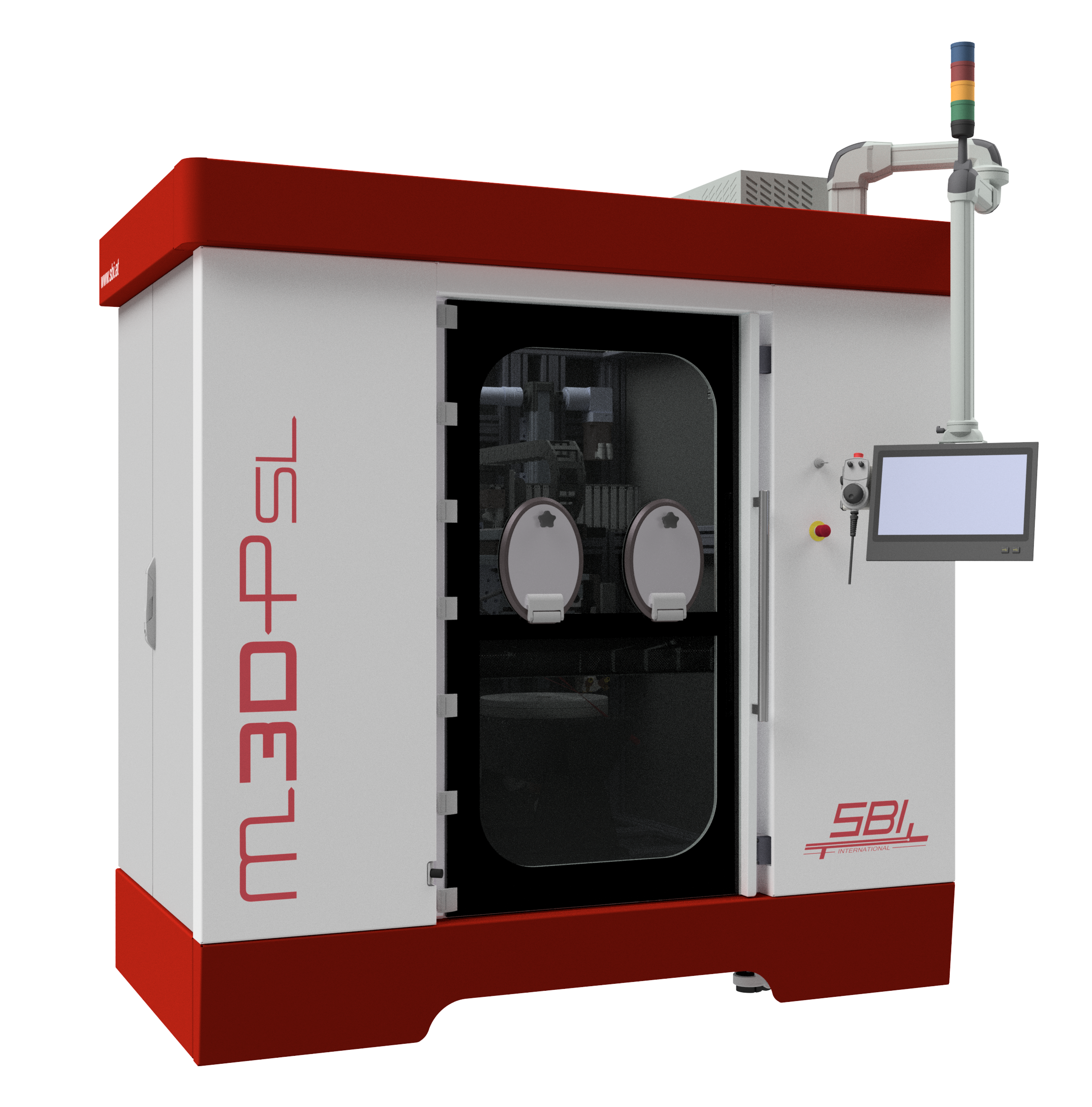
With the M3DP scientific line SBI offers a flexible Additive Manufacturing System for smaller production volume, research groups, universities and creative users, that are interested in pushing technology borders.
M3DP | M3DP-SL | |
Dimensions | 5000x2400x4200mm (X-Y-Z) | 1700x1400x2600mm (X-Y-Z) |
Build volume | 2000x600x600mm (X-Y-Z) | ø400x500mm (X-Y-Z) |
Mass | 6.500 kg | 3.500 kg |
max payload | 650 kg | 250 kg |
airtight system | yes - optional available | yes - standard |
feedstock | metal wire & powder single and multi-feeding options |
metal wire & powder single and multi-feeding options |
energy source | plasma arc (PMD) | plasma arc (PMD) |
typical deposition rates | 10 kg/h for nickel base alloys 5 kg/h for titanium |
10 kg/h for nickel base alloys 5 kg/h for titanium |
PMD is a “near net shape” process and means that post processing like lathing and milling are almost always necessary. The process works with all fusion weldable metals like steel, nickle-base alloys, titanium, aluminium,...
Compared to other DED and LMD systems, the M3DP offers high feed and build up rates for a variety of metal feedstock.
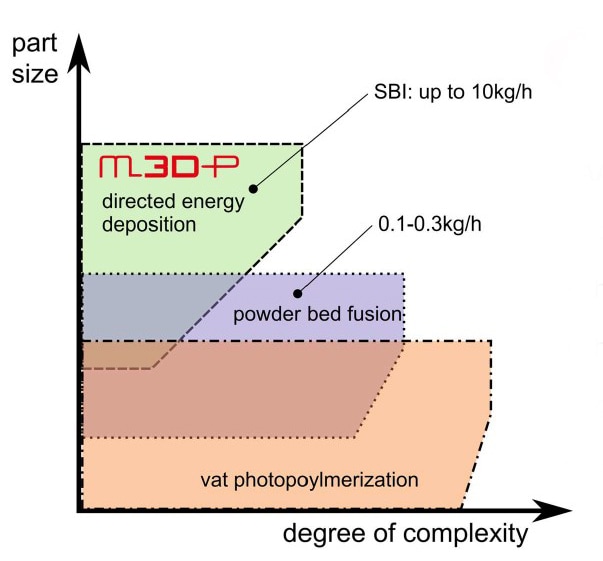
Our AM technology used for the M3DP is a Direct Energy Deposition (DED) process called Plasma Metal Deposition (PMD)
PMD is an AM technology for:
- big parts with good structural integrity
- high deposition rates
- high versatility, works with both wire and powder
- good scalability
- excellent economical potential