More than a box of metal sheet!
Liquid natural gas tanks in are high-tech monsters inside a Tanker. They need to handle huge temperature differences from -160°C to +40°C or more, if still empty. Also the volume changes during transportation, as liquid gas continuously evaporates. To compensate these severe environmental impacts, the walls are engineered to compensate for these changes.
Curled steel sheets are welded together, not an easy task for automated processing. The weld seam needs to be gas tight. Specially designed plasma welding systems from SBI are used to master this challenge in an extremely high precision. In the process the primary metal membrane with a thickness of only 1mm is welded onto the secondary layer, that is integrating the cooling channels for insulation.
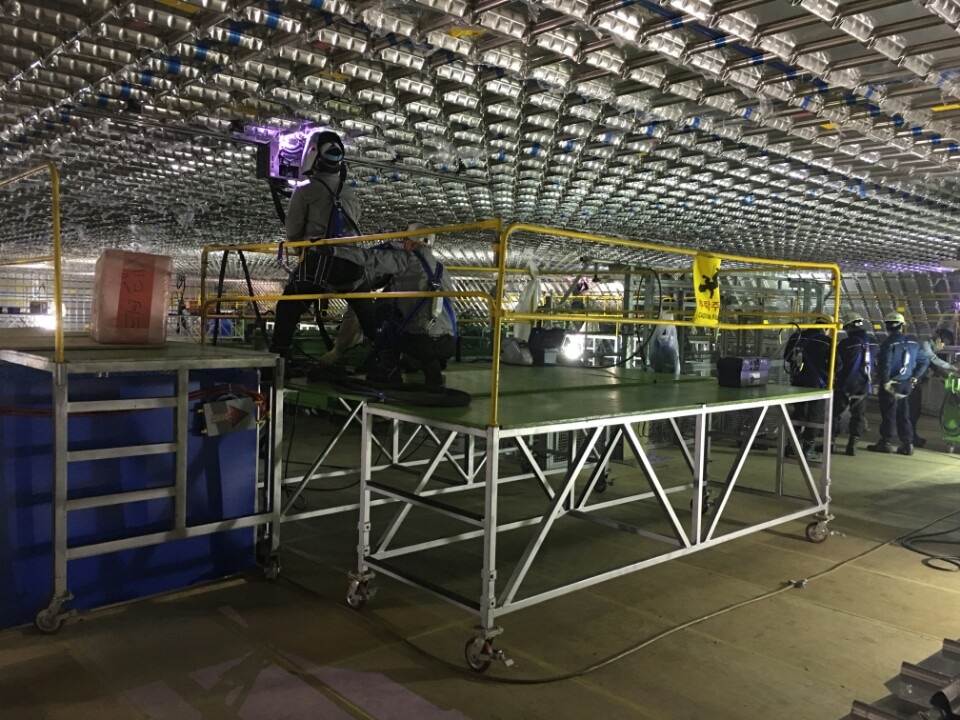