Welding of tanks for wine storage and transportation
In the processing & handling of beverages, stainless steels are the favoured materials to use. Thanks to their good durability against corrosion and their low affinity to release alloying elements, stainless steels are a superb choice for this task. Plasma Spot Welding is used to join stainless steels in an economic way, the focused plasma arc and the additional shielding gas enable fast and safe welding procedures.
Wine tanks
The conditions in wine tanks are normally harsh due to the occurance of wine-acid, melic-acid and citric-acid and are one of the reasons why to use stainless steels i.e. 1.4301 or 1.4404 for this job.
Additionally in modern wineries the wine also has to be tempered, depending on its stage of maturation. For this reason the walls of the wine tanks are double layered so they can be flushed with heated resp. cooled water.
This is achieved by plasma spot welding of two sheets of stainless steel in a regular pattern. After the spot welding is done a hydrostatic pressure is applied between the two joined sheets. The pressure inflates the two sheets which expand and create a channel.
Due to the superior welding properties of the Plasma Spot Welding process, the spot weld has enough strenght and ductility to enable the hydrostatic deformation process.
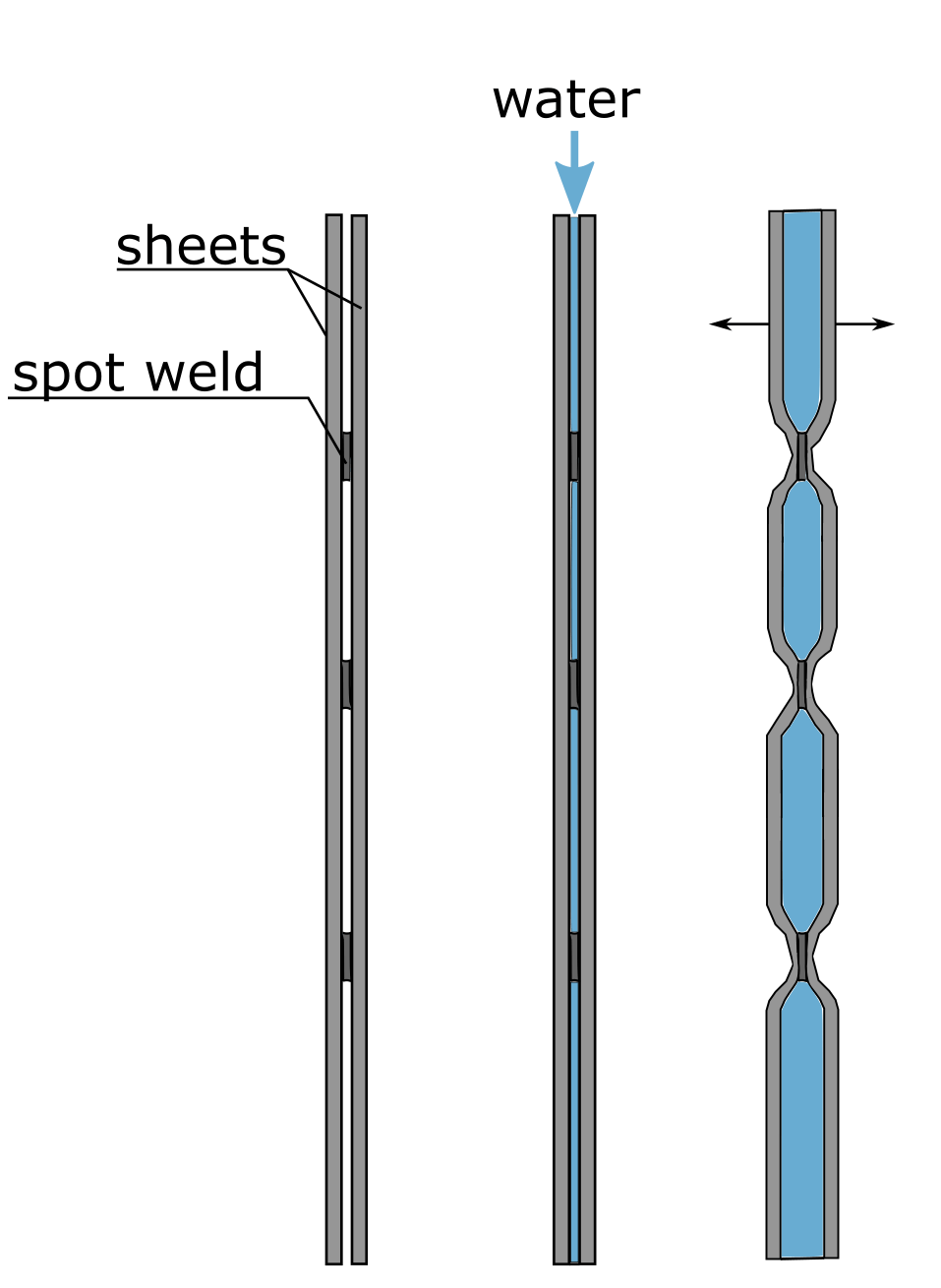
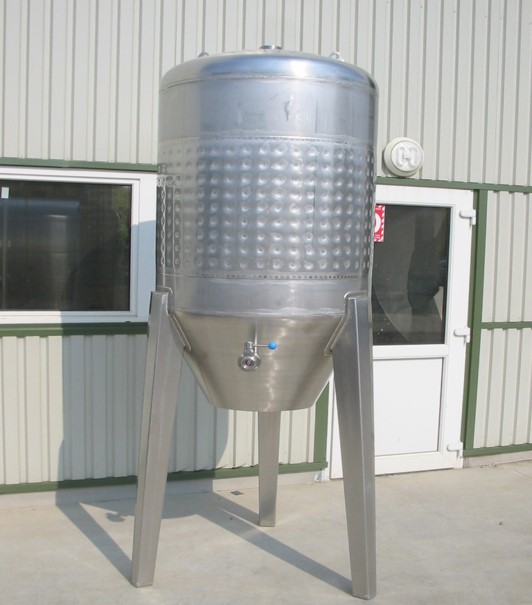