Konzept zur Massenproduktion von Automobilteilen mittels Plasma Metal Deposition
In der Automobilindustrie wird die additive Fertigung (AM) typischerweise dort eingesetzt, wo die Kosten pro Teil als Prototyping oder Hochleistungsteile weniger relevant sind.
Die Plasmametallabscheidung (PMD) ermöglicht die Herstellung großer Teile (> 1 m). Aufgrund der hohen Abscheiderate, Skalierbarkeit und geringen Investitionskosten kann es als kosteneffizientes Verfahren angesehen werden. Diese Studie präsentiert ein Konzept für die Massenproduktion (> 10.000 Teile / Jahr) additiv hergestellter Getriebehalterungen, um das Potenzial von PMD aufzuzeigen.
Um die Produktionseffizienz zu optimieren, werden verschiedene Konzepte bewertet, beispielsweise Hybridkomponenten, bei denen die Grundplatte als integraler Bestandteil der Halterung verwendet wird. Um die Sekundärbearbeitung zu minimieren, werden nur Funktionsflächen bearbeitet.
PMD verwendet einen Plasmabogen hoher Dichte als Wärmequelle, um das Grundmaterial und das Füllmetall zu schmelzen. Durch Injizieren von Pulver in den Fokus des Plasmas und durch Bewegen des Brenners auf bestimmten Wegen während des Prozesses wird die dreidimensionale, netznahe Formkomponente erzeugt. Verschiedene Verarbeitungsparameter werden untersucht. Um die Qualität des abgeschiedenen Materials und des Prozesses zu bewerten, wird ein Hochzyklus-Ermüdungstest durchgeführt.
In einem Batch-Prozess, bei dem viele Teile gleichzeitig hergestellt werden, funktioniert dies nicht mehr - ein 2,5-D-Prozess wird bevorzugt. Aus der ursprünglich gegossenen Getriebehalterung wird in einem ersten Schritt der Konstruktionsraum definiert . Schließlich wird das Design der Klammern für PMD abgeleitet und unter Verwendung einer topologischen Optimierung in Bezug auf die Einschränkungen des PMD-Prozesses bewertet. Ziel der Simulationen ist es, die Masse zu reduzieren, indem gleichzeitig die strukturelle Integrität des Teils erhalten bleibt. Dabei wird das Volumen als Auslegungsvariable und die Verformungsenergie als Zielfunktion definiert. Die Ergebnisse der FEM-Analyse zeigten, dass die Masse im Vergleich zum gegossenen Design um 1/3 reduziert werden kann, während eine ähnliche Steifheit vorliegt. Um das ursprüngliche Bracket-Design mit dem PMD-Design zu vergleichen, wird die maximale Verschiebung mit der Masse der Brackets skaliert, wie aus der folgenden Tabelle hervorgeht.
Die Halterungen sind auf einer Grundplatte angeordnet. Für diesen Anwendungsfall wird eine Charge von 9 Klammern gleichzeitig hergestellt, aber mit der vorhandenen PMD-Maschine mit einer Bauplattform von 2 x 1,5 m ist eine Chargengröße von> 160 möglich, wenn eine größere Argonbox implementiert würde.
Bracket casting | Bracket PMD | |
Max. displacement [mm] | 0,12 | 0,15 |
Volume [mm³] | 194199 | 127828 |
Mass [g] | 1505 | 997 |
Factor_max [mm*g] | 173 | 153 |
Table: Results of FEM design optimisation
Zur Entnahme der Halterung wird das Wasserstrahlschneiden eingesetzt, da dieses effiziente Verfahren die Entnahme aller Teile einer Charge in einem Fertigungsschritt ermöglicht. Die Grundplatte wird dann in das Teil integriert.
Effizienz und Massenproduktion
Um die Idee der Massenproduktion mit PMD vollständig zu erfassen, wäre es notwendig, alle relevanten Einflussfaktoren auf die Kosten sowohl für die traditionelle Massenproduktion als auch für das PMD-Verfahren zu erfassen. Dennoch ist es möglich, einige Faktoren wie unten dargestellt abzuschätzen.
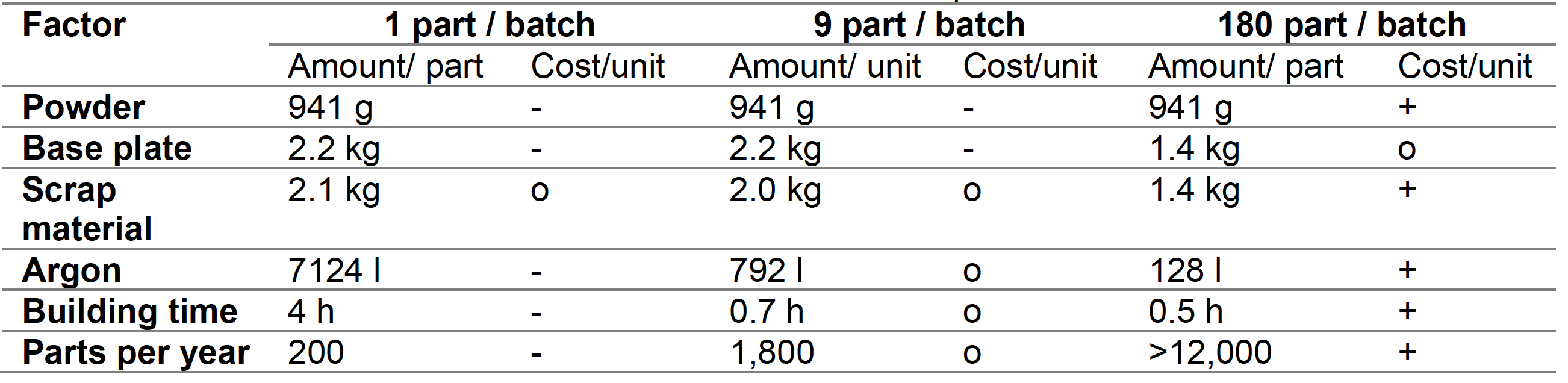
Die Menge des verwendeten Pulvers ändert sich nicht mit der Losgröße, aber die Materialkosten sinken durch den Großeinkauf. Bei Verwendung einer großen Bauplattform kann die Anordnung der Teile weiter optimiert werden, um Material und Kosten zu sparen. Da die Grundplatte in das Teil integriert ist, hat dies einen erheblichen Einfluss auf die Menge an Ausschussmaterial. Der Verbrauch von Argon skaliert mit der Größe des Volumens der Schutzkammer. Eine größere Chargengröße - die Kammer für eine 180-teilige Charge ist dreimal so groß wie für eine 9-teilige Charge - und eine optimierte Nutzung des Bauraums verringern daher den Argonverbrauch pro Teil. Das Einrichten der PMD-Maschine dauert etwa 2 Stunden, fast unabhängig von der Losgröße. Der Bau großer Chargen verringert diesen Einfluss.
published @EUROPM2020 conference, RHP-Technology GmbH, John Meuthen et al.
The authors thank the European Commission for financial support through H2020 grant agreement n°768612 (SUPREME project within SPIRE program).